Defects often caused by improper forging process
Jun 14,2024
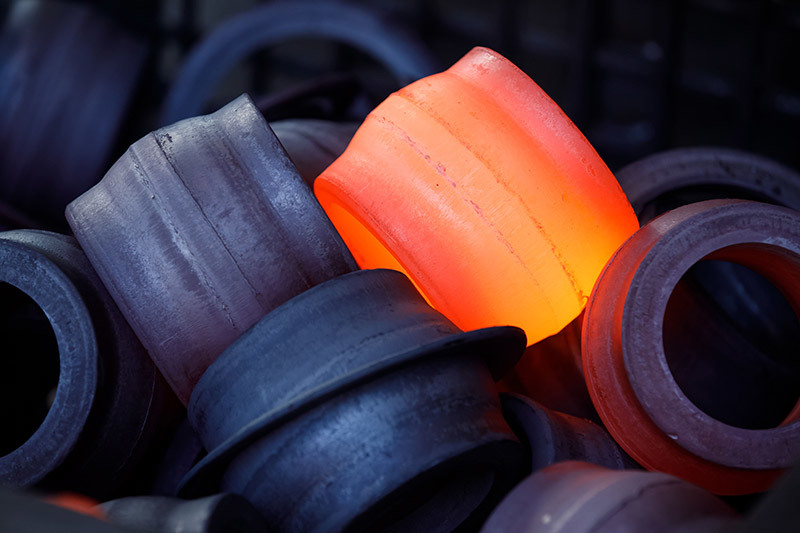
Large grain size
Large grains are usually caused by high initial forging temperature and insufficient deformation degree, or high final forging temperature or deformation degree falling into the critical deformation zone. Excessive deformation of aluminum alloy, resulting in texture formation; When the deformation temperature of high-temperature alloys is too low, the formation of mixed deformation structures may also cause coarse grains. Coarse grain size will reduce the plasticity and toughness of forgings, and significantly decrease their fatigue performance.
Uneven grain size
Uneven grain size refers to the condition where certain parts of a forging have particularly coarse grains, while others have smaller grains. The main reason for uneven grain formation is the uneven deformation in various parts of the billet, which leads to varying degrees of grain fragmentation, or the degree of deformation in local areas falling into the critical deformation zone, or local work hardening of high-temperature alloys, or local grain coarsening during quenching and heating. Heat resistant steel and high-temperature alloys are particularly sensitive to uneven grain size. Uneven grain size will significantly reduce the durability and fatigue performance of forgings.
Cold hardening phenomenon
During forging deformation, due to low temperature or too fast deformation speed, as well as too fast cooling after forging, the softening caused by recrystallization may not keep up with the strengthening (hardening) caused by deformation, resulting in the retention of cold deformation structure inside the forging after hot forging. The presence of this organization improves the strength and hardness of forgings, but reduces plasticity and toughness. Severe cold hardening may cause forging cracks.
crack
Forging cracks are usually caused by significant tensile stress, shear stress, or additional tensile stress during forging. The crack usually occurs in the area with the highest stress and thinnest thickness of the billet. If there are micro cracks on the surface and inside of the billet, or if there are structural defects inside the billet, or if the thermal processing temperature is improper and reduces the material's plasticity, or if the deformation speed is too fast or the degree of deformation exceeds the allowable plasticity pointer of the material, cracks may occur in processes such as roughening, elongation, punching, expanding, bending, and extrusion.
Cracking
Forging cracking is a shallow turtle shaped crack on the surface of a forging. The surface under tensile stress in forging forming (such as unfilled protrusions or bent parts) is most prone to this defect.
The internal causes of cracking may be multifaceted:
(1) Excessive amount of fusible elements such as Cu and Sn in the material;
(2) When heated for a long time at high temperature, copper precipitates, coarse surface grains, decarburization, or surfaces that have been heated multiple times on the surface of the steel material;
(3) The sulfur content of the fuel is too high, and sulfur seeps into the surface of the steel material.
PREVIOUS:
Contact Us
E-mail :
hongxinjingduan@163.com
Phone/WhatsApp:
+86-13932867896, +86-15603187896
Address:
Longhua Town, Jing county, Hebei Province, China